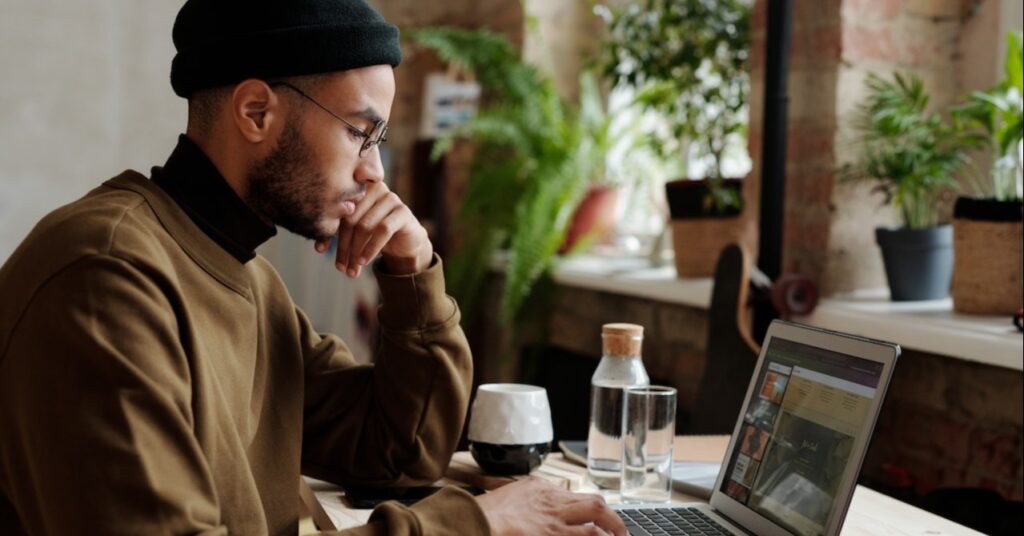
How to Choose an Online MBA
Online MBA programs make their degrees available to everyone everywhere, [...]
Imagine a professional swimmer’s body with pure muscles and no fat whatsoever. No bulk, either; we’re not talking about the torso of a bustling bodybuilder here.
Lean businesses strive to be exactly like that swimmer. They seek to develop just enough muscle while remaining free of fat and extraneous capacity. Fat and overgrown muscles are the wastes that organizations discard under lean methodologies.
Lean professionals have identified seven categories of waste that do not add direct value to the products or services generated. These seven wastes are (not necessarily in the order of importance):
Many professionals use the acronym TIMWOOD to remember this list. There is even a song about it; watch it here.
Some practitioners recently added an eighth waste to the list: non-utilized talent. DOWNTIME is the acronym for the list of eight (defects, overproduction, waiting, non-utilized talents, transport, inventory, motion, excessive processing).
Regardless of which list and acronym you favor, you should familiarize yourself with the types of waste Lean Six Sigmaaims to eliminate. Let’s take a closer look.
In any operation, physical materials move between locations. If we are talking about the retail industry, consumer goods travel between distribution centers and stores, and within the stores, they move from the stockroom to the shelves. In manufacturing companies, the raw materials go on trucks from the suppliers to the factory, where parts move from the warehouse to the workstations to get assembled. From a lean perspective, transportation is a necessary evil because it does not add direct value to the product or the service.
Companies must minimize the movement of goods between different facilities or between workstations. There are analytical techniques for the optimization of goods movement processes. For example, logistics companies use algorithms to ensure they use vehicle space optimally and travel along the shortest route possible. Lean professionals design facility layouts that require minimum movement between receiving areas, stocking locations, workstations, and shipment areas. Traditional conveyor belts and more recent technologies such as automated guided vehicles (self-moving forklifts, shelf-carrying robots) or remotely controlled forklifts offer great utility for efforts towards minimizing transportation activities.
University and Program Name | Learn More |
Stevens Institute of Technology:
Online Master of Business Administration
|
|
The University of Tennessee:
Online Master of Business Administration
|
When listed as an asset, inventory may look benign on a balance sheet. However, from a cash flow or opportunity cost perspective, the less inventory, the better. In business slang, cash is king; the stock sitting on your floor is cash tied to goods waiting for their turn. It occupies space with no immediate value to your customers, preventing you from investing the equivalent cash in a dividend-yielding financial opportunity. That’s one reason companies should minimize inventory. But LSS professionals have another excellent justification for getting rid of excess stock.
Many companies regard inventory as a buffer between processes, decoupling them from each other to make each process independent of temporary breakdowns and failures in other connected ones. Sounds rational, right? Paradoxically, LSS practitioners have shown that this decoupling of operations is a considerable obstacle to the continuous improvement approach.
If a company wants to create an environment of continuous improvement, it must train its employees to develop a matching mindset organically. One requisite for this organic growth is generating a sense of urgency toward the need for improvement.
Imagine an assembly line with a lot of parts resting between workstations. If a worker gets a piece to process and notices that it is faulty, they would most likely leave the faulty one aside and pick another from the pile. It will probably be a long time—if ever—before someone puts some effort into figuring out what the problem was with the faulty part, what caused it, and what needs to be done to prevent it. The result is hidden problems.
With low-inventory workstations, workers do not have the luxury of putting the faulty parts aside. Each piece becomes valuable; thus, improving the processes becomes vital for preventing the generation of defective parts.
From an LSS point of view, inventory hides problems and inhibits continuous improvement efforts. That is why it is one of the seven wastes.
How many yards does a factory worker walk during a shift to get the tools or materials necessary to complete the tasks efficiently? How often would a solderer stretch their hands to reach the required equipment to work on the printed circuit boards? Are those movements adding any value to your products or services? Are the customers willing to pay you for those unnecessary motions of the employees? Are those any good for the employees?
Clearly, your answer to the last three questions would be straight “no’s.”
Organizations must design facility layouts and workstations in a way that requires minimum movement of employees. An ergonomic design for workbenches (seats, desks, monitors, shelves, tools, bins, etc.) is, first and foremost, essential to keep a healthy workforce while minimizing non-value-adding motions.
We discussed one aspect of waiting when dealing with the inventory category. Parts in the inventory are waiting to be processed, adding no direct value to the products or services we offer customers.
The other aspect of waiting is the result of poor scheduling. Think of a situation when you are waiting for the mechanic to replace your car’s dead transmission. The shop told you to bring the auto on this day and promised to get it ready the next day. You call them the next day to inquire about what time to be there and are frustrated with the response that you can only pick it up one day later. It turns out that the shop personnel put the wrong date on the purchase order for your new transmission system, which did not arrive soon enough to get your car fixed today.
This exact scenario can happen in the operations of organizations if they fail to generate smooth schedules for required parts of labor. Suppose only two operators can run three different pieces of equipment, and the scheduler plans to run all three simultaneously. In that case, one job will have to wait, which might result in unhappy customers, especially when you promised them all three orders on the same day.
Would you pay an extra $10 for a small cup of coffee only because the disposable cup has a photo of you printed on it? I assume not.
Businesses must put enough effort into understanding their clientele’s needs to offer the right products and services to fulfill those needs. All product or service features your customers deem necessary should be part of the design. Any feature that doesn’t add value to your offering in the eyes of the customer is a waste.
Organizations following the LSS approach must maintain open communication channels with their customers to determine the ideal product/service designs without any fancy features that offer little or no real value.
Overproduction is directly related to the inventory waste category. Minimizing inventory is crucial for the success of LSS, which insists that businesses should only produce according to actual customer demand instead of the forecast. Companies can achieve this using a pull production philosophy (which should be the subject of a separate article). Here, the critical thing to understand is the dilemma of reduced utilization rates during low-demand periods.
Operations managers might consider idle workstations due to insufficient demand a waste. Although it might look counterintuitive, suspending a workstation when there is not enough demand is the right thing to do if you do not want to create excess inventory, which, as we saw, hides production problems. Obviously, having idle time on the shop floor is not desired, but it offers other opportunities. For example, LSS professionals proactively plan for idle times, scheduling employee training and preventative maintenance for equipment.
Defects are parts or products that do not meet the design specifications; they are either scrapped or reworked. It is not hard to guess why defects are considered waste. They are costly and create distress in the system and flaws in the production schedule. When operations run on minimum inventory, defects become even more critical. Because there is not much buffer between workstations, all parts in the buffer become valuable and defects are not tolerated. That is why LSS professionals repeat the motto “do it right the first time,” as employees have little leeway to fix mistakes without causing the whole assembly line to stop.
Statistical process control is a handy tool to monitor processes continuously and intervene when there are signs the process might start generating defective parts.
B
efore we end, why don’t we say a few words about the newest addition to the original seven wastes list? LSS professionals noticed the waste created when they did not utilize the most valuable resources of an organization—namely human resources—to its fullest potential. The title is self-explanatory in that sense. LSS organizations must find the optimal ways to develop their workforce through upskilling and proper career planning and employ them in positions where they can contribute the most.
(Last Updated on February 26, 2024).
Questions or feedback? Email editor@noodle.com
Online MBA programs make their degrees available to everyone everywhere, [...]
In 2004, Burton D. Morgan Foundation and other Cleveland organizations [...]
International marketers have to consider local language(s), local norms and [...]
Many aspiring entrepreneurs understand the basic idea that the firm [...]
Six Sigma drives efficiency at innumerable manufacturers, service providers, healthcare [...]
Categorized as: Operations Management, Business & Management