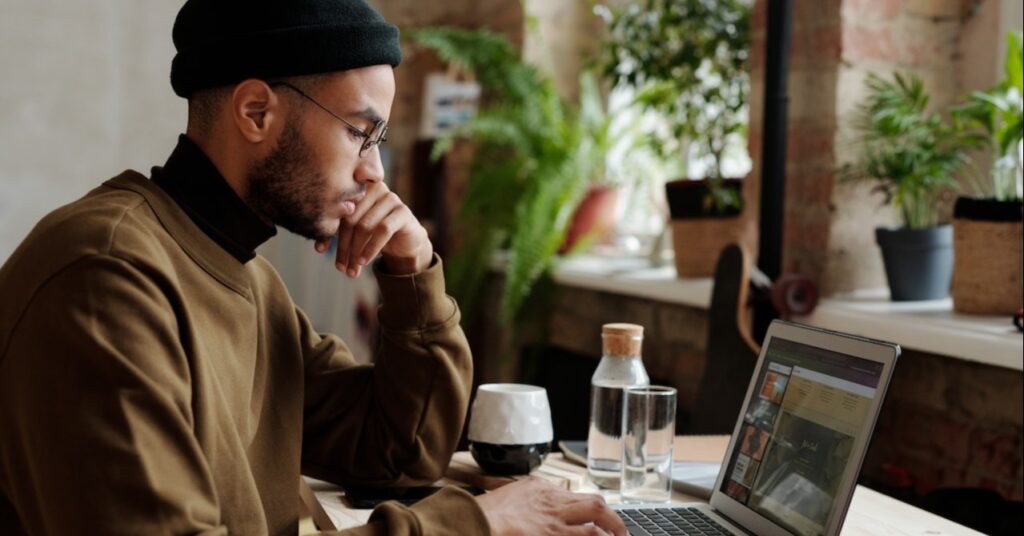
How to Choose an Online MBA
Online MBA programs make their degrees available to everyone everywhere, [...]
Reports indicate that the commercial aviation industry has witnessed significant growth in the 21st century. Research further suggests that aircraft fleets are expected to grow by 40 percent by 2032. Passenger load factor, flight frequencies, and route selections have increased rapidly, generating significant revenue gain but, unfortunately, low margins.
Low margins specifically resulting from aircraft maintenance operations present challenges when formulating a business model for aviation maintenance repair and overhaul (MRO) facilities. That’s critical, because an aviation MRO facility’s strategy provides the competitive playbook by which an organization executes its business plans and establishes competitive scope.
MRO facilities present numerous difficulties. The most significant include lowering maintenance costs and meeting contractual downtimes for scheduled aircraft maintenance operations. Poor quality attributes performed during scheduled maintenance and processes promote worker errors that increase operating costs. Errors tend to induce unstable maintenance operations that drive up failure costs; these costs, if not controlled, can potentially render a company insolvent.
The onset of the global pandemic pressured aviation business leaders to develop new and creative ways to sustain competitive advantage. This bow wave—so named after the sea waves that impact the bow of a ship and send a ripple effect through the ship’s body (not because the graph of the wave is shaped like a bow)—forced business leaders to explore other business methodologies that could drive down operating costs and increase margins. They needed to adopt an agile business posture while modifying or rejecting organizational behaviors that continue the status quo.
University and Program Name | Learn More |
Pepperdine University:
Online Master of Business Administration
|
|
Stevens Institute of Technology:
Online Master of Business Administration
|
|
Merrimack College:
Master of Science in Leadership
|
|
Merrimack College:
Master of Science in Management
|
|
The University of Tennessee:
Online Master of Business Administration
|
Aviation service companies aim to improve the customer’s experience through decreased maintenance costs and improved turnaround times. To lower maintenance costs, internal and external failures must be monitored and managed. Failures tend to manifest themselves as waste, incurring costs that impact the bottom line.
This problem is not isolated to the aviation industry. Most businesses find that the following can constitute up to 55 percent of their costs:
All this waste represents capital thrown away due to poor business processes. Lean Six Sigma represents an agile business solution to the waste problem.
Lean Six Sigma effectively addresses waste in the way people work. It eliminates waste from processes (which essentially constitute everything a business does), speeding them while increasing efficiency, productivity, and flow. It is especially effective in promoting efficiency: when businesses implement Six Sigma processes correctly, they experience no more than 3.4 defects per million opportunities, a 99.99 percent positive quality outcome rate.
Six Sigma delivers its results through the use of data, applying statistical tools to raw data to discover insights and drive process improvements. It can impact business philosophy, business tools, strategy, and the formulation of value propositions for differentiation.
For aviation MRO facilities to maximize profits, business leaders needed to identify and control waste. That, in turn, decreases poor quality occurrences at the source. When quality escapes are prevalent, the estimated staff hours for conducting investigations, including increased management oversight, is approximately $700,000 (1 percent) added accumulated cost, based on U.S. commercial aircraft data.
Lean Six Sigma applies to every industry function, a one-size-fits-all business improvement methodology originally applied to manufacturing. Today, it has expanded to the petroleum industry, healthcare, information technology, aviation/aerospace, finance, logistics, automotive, and engineering industries. Many of these industries have adopted Six Sigma as a value proposition and for the introduction of new product development of services and products.
Lean Six Sigma (LSS) encompasses various certification belts like martial arts; these include Certified Master Black Belts, Black Belts, Green Belts, and Yellow Belts. Practitioners ascend levels and earn higher-value belts by acquiring competency and experience through training and practice.
Master Black Belts (MBBs) work with business champions on LSS infrastructure and project selections. MBBs can provide LSS training, coaching, and mentoring to Black Belts and Green Belts. They work on business projects as full-time or part-time LSS project leaders and provide mentoring and coaching to LSS Green Belts on the D-M-A-I-C process, the structured and disciplined LSS process that stands for:
Green belts are project owners who use LSS tools to bring continuous improvement in the way work is performed.
LSS Yellow Belts typically work as project members. They are often assigned to work with LSS Green Belts on various work streams that lead to process improvement outcomes. LSS Yellow Belts are business change agents with the basic knowledge of DMAIC and the tools of Lean.
All work performed in the aviation MRO industry is a process, and every operation is subject to variation, especially when people are a factor in the equation. Variation is the enemy and the driving force behind individual decision-making; it increases the cost of quality in aviation maintenance processes. If the variation is not identified and controlled during maintenance activities, the cost of delivering high-quality services and products will continue to be a problem.
LSS Yellow Belts are foot soldiers who recognize and identify waste. The Breakthrough Management Group Inc. (BMGI) identifies three rules of waste:
LSS Yellow Belts address and tackle eight types of business waste:
LSS Yellow Belts seek to eliminate the chaos and delays endured when workers search for tools, search for information, or fail to execute a task correctly the first time. They employ a litany of business tools to accomplish their responsibilities. These include:
LSS Yellow Belts apply statistical control to business processes. They are instrumental in the overall business change paradigm, managing small workstreams as deliverables. Most consider their Yellow Belt work a form of training necessary to advance to the Green Belt level.
A company that adopts methodologies such as Lean and Six Sigma never ceases to improve. Striving for perfection is, in fact, one of the five principles of Lean: one never stops looking at processes for improvement. Lean speeds processes by eliminating waste and creating flow, while Six Sigma reduces variation in the way that we work, thereby increasing quality so that production achieves nor more than 3.4 defects per million opportunities (DPMO). The mindset drives improvement through small daily incremental adjustments to business processes.
(Last Updated on February 26, 2024).
Questions or feedback? Email editor@noodle.com
Online MBA programs make their degrees available to everyone everywhere, [...]
In 2004, Burton D. Morgan Foundation and other Cleveland organizations [...]
International marketers have to consider local language(s), local norms and [...]
Organizations must design facility layouts and workstations in a way [...]
Many aspiring entrepreneurs understand the basic idea that the firm [...]
Categorized as: Business Administration, Operations Management, Business & Management