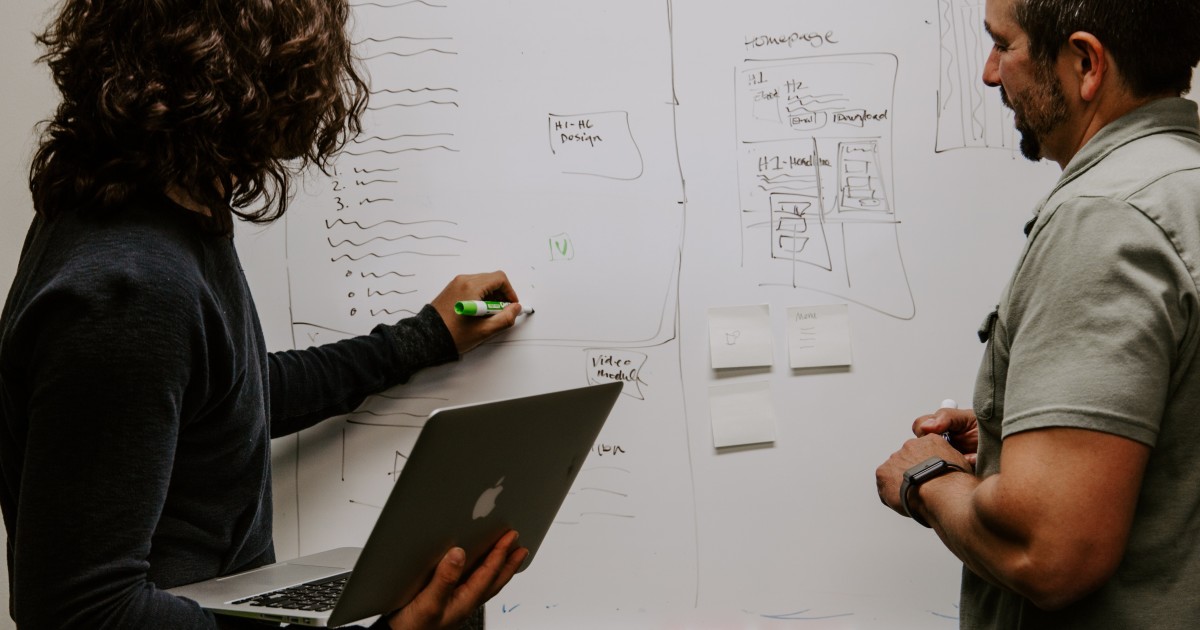
How to Become a Logistics Analyst
Logistics professionals, including analysts, earn good money and love their [...]
Key performance indicators—KPIs to the acronym-loving business world—provide a roadmap for improving supply chain processes and outcomes. Whether looking to revamp warehousing policies, tighten the customer order cycle time, or approach the perfect order rate, KPIs provide the data needed to drive improvement. KPIs vary based on industries, business types, and business sizes, meaning supply chain managers must individually decide which indicators best serve their desired outcomes.
Regardless of chosen KPIs, however, the best offer objective evidence based on measurable data. With this data at hand, managers can set targets to increase profit margins, improve fill rates, and raise on-time delivery rates.
This article explores the top nine supply chain key performance indicators.
Operators across the supply chain management universe utilize several common KPIs. These include:
Cash-to-cash cycle time is a common KPI for supply chain managers, and for good reason: this metric examines how long it takes to convert supplies into sales. Cash-to-cash cycle time plays an important role in that it provides valuable data on the amount of cash-flow carry needed and highlights the efficiency—or inefficiency—of current practices.
Calculating cash-to-cash cycle time requires adding days of payables and days of inventory together before subtracting days sales outstanding. The lower the result, the better cycle time a company produces.
Both precise estimated times of arrival (ETAs) and on-time order deliveries function as part of the larger perfect order KPI. This compound measurement also includes damage-free order-fill delivery rates as well as accurate documentation. Given how much information this KPI can supply as a performance measurement, supply chain managers regularly rely on it for insightful data. In addition to determining whether clients are receiving their packages when stated, this KPI also provides information on accurate packaging procedures, including both correct items and proper documentation.
Calculating perfect order is rather easy. Supply chain managers simply subtract the number of orders with errors from the total number of orders before dividing this number by the total number of orders. From there, simply multiply that number by 100.
For a company to function effectively, it must collect payments from customers in a timely manner. Failing to do so can negatively affect cash flows, making it hard to purchase raw materials for product development and cover other operating costs. Businesses with low rates of DSO typically have healthy financial standing and sound customer billing practices. Companies with high days sales outstanding may struggle with cash flow and have less healthy bottom lines.
Calculating days sales outstanding involves dividing accounts receivable by sales before multiplying this figure by the number of days in the current period.
An oversupply of inventory likely seemed like a bad thing pre-pandemic, but these days supply chain managers are rethinking how many days worth of inventory supply makes sense for their businesses. With supply chains for many industries taking an unpredictable path over the last few years, many managers are leaning toward tying up a slightly larger percentage of cash flow.
Even so, inventory days of supply are considered a strong KPI when on the lower side as it signals lean and effective management. Calculating this indicator involves dividing the amount of inventory available by average daily inventory sales.
Also known as inventory turnover, the carrying cost of inventory functions as part of the KPI dashboard for countless supply chain managers. This benchmark provides the data needed to identify whether a company is properly minimizing and managing the cost of keeping inventory on hand. Some of the factors influencing this figure include the costs of storing, shipping, insuring, and handling items before inventory sells.
Calculating the carrying cost of inventory involves multiplying the average inventory value by the inventory carrying rate. Most carrying costs are approximately one-fifth of overall inventory expenses, but this figure ebbs and flows based on industry.
With many companies placing emphasis on sustainable boxing materials usage and more environmentally-friendly shipping processes, the uses—and misuses—of packing materials have received closer inspection in recent years. It may seem like a negligible amount, but overusing packing materials by even an extra sheet of bubble wrap or few extra grams of weight per package can add up to significant budget overages, both in materials and freight costs.
For supply chain managers looking to monitor packing material overages, the most effective method is to measure existing counts or weights. From there, setting benchmarks for lowered usage can help managers identify how much money can go back to the budget over time.
The reason a consumer lists for returning a purchased item can tell managers a lot about not only customer satisfaction but also order fulfillment issues. For instance, an uptick in reports about damaged items signals that supply chain processes around packing need to be addressed. Meanwhile, if more customers begin returning items due to no longer needing them, issues around the timeframe of delivery could be the culprit.
Using reasons for return as a KPI helps managers easily identify patterns. Subtracting returns based on individual reasons from the total number of orders allows these professionals to find the problem and update processes that rectify the issue.
Inventory velocity identifies how much inventory is needed for the next sales period. This indicator proves especially useful for managers looking to better mirror supply to demand and avoid excessive stock that takes up space and increases inventory carrying costs. While requirements vary from business to business, inventory velocity measuring between 60 to 70 percent is preferable.
To calculate inventory velocity, managers can use the average inventory available to divide the cost of goods. To understand starting and ending inventory figures for each sales period, take the original figure and divide by two.
If you’ve ever paid attention to the amount of time it takes from placing an Amazon order to receiving notification that it has shipped, you’ve thought about the pick-and-pack cycle time. This refers to the specific amount of time it takes from when a worker picks up a recently sold item to when the shipping process begins.
By measuring the individual components of this cycle, managers can identify areas of inefficiency within the chain and introduce policies to correct them.
The most effective supply chain managers possess advanced skills in data analysis, inventory management, and supply chain operations, all of which they use to optimize logistics within their companies. While plenty of roles in this discipline exist for professionals with a bachelor’s degree, those who want to reach the upper echelons of the field often decide to pursue a graduate degree.
Learners who decide to go down this path can choose from two options. The University of Tennessee-Knoxville offers both an MS in supply chain management and an Executive MBA in supply chain management in accelerated formats. The MS option requires 18 to 24 months to complete; students graduate from the Executive MBA in just one year. Within both curricula, degree-seekers learn how to isolate the right KPIs for individual businesses, identify and minimize supply chain costs, optimize efficiency and accuracy, and stay nimble when handling customer demands and customer expectations.
When deciding which graduate degree best meets your career needs, it’s important to carefully review both expectations and outcomes. The average learner who enrolls in the MS in supply chain management typically possesses seven years of work experience, while those applying to the Executive MBA in supply chain management possess ten or more years of managerial experience.
Questions or feedback? Email editor@noodle.com
Logistics professionals, including analysts, earn good money and love their [...]
Categorized as: Supply Chain Management, Business & Management