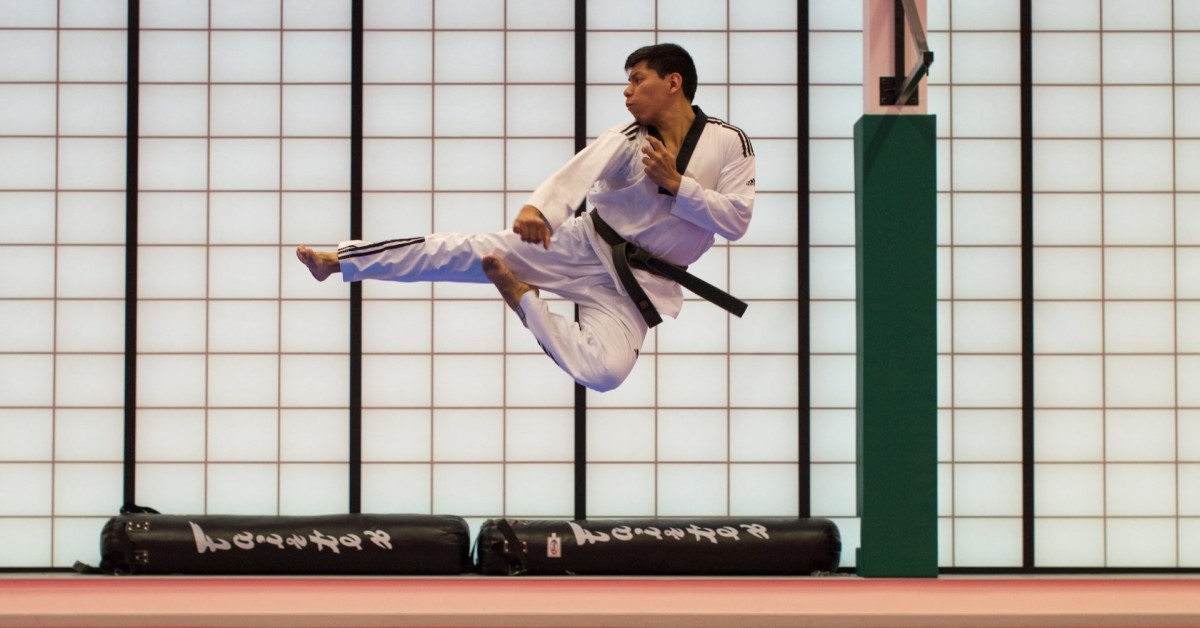
What Are the Levels of Lean Six Sigma?
You can earn Lean Six Sigma certification at the white [...]
Lean management aims to eliminate the waste in processes by removing activities that do not add value to customer expectations. Six Sigma focuses on minimizing defects by reducing process variations. Although these two continuous-improvement methodologies started their journey separately, it didn’t take long for practitioners to realize that they work together like a charm. Since the early 2000s, countless organizations have been improving their processes using Lean Six Sigma (LSS) tools.
LSS relies on a step-by-step improvement approach called the Define-Measure-Analyze-Improve-Control cycle, often abbreviated to the acronym DMAIC methodology. It’s so popular that songs have been written about it (you’ll probably recognize the melody).
So, how does DMAIC work? Let’s study all five phases of this intuitive and practical methodology.
LSS emphasizes continually improving production and business processes to eliminate waste and minimize variability. It is also a bottom-up approach that justifiably assumes that the best improvement ideas come from those with first-hand knowledge of the job.
If an organization has created a culture that empowers and equips employees with the skills to improve the existing processes in which they are directly involved, those workers should propose numerous improvements to those processes. Implementing them all is usually not viable due to time and resource constraints.
The define phase offers a mechanism to assess and prioritize proposals based on a cost-benefit analysis. Management examines the improvement ideas applying such criteria as:
The company decides which improvement proposal to implement in a problem statement. The team now has the necessary information to move to the next DMAIC phase, which is the measure phase.
University and Program Name | Learn More |
Pepperdine University:
Online Master of Business Administration
|
|
Stevens Institute of Technology:
Online Master of Business Administration
|
|
Merrimack College:
Master of Science in Leadership
|
|
Merrimack College:
Master of Science in Management
|
|
The University of Tennessee:
Online Master of Business Administration
|
The team responsible for an LSS project needs data that explain the problems they are trying to solve. As a colleague of mine is fond of saying, “What gets measured, gets done.”
The measure phase is about determining what inputs the team needs to analyze the current state of the processes. These indicators will serve as a baseline against which the team can assess their achievements in the following phases.
Organizations use software systems to record everyday business transactions that include sales, purchasing, HR, accounting, production control, inventory management, and shipments. Ideally, a single, sophisticated database integrates the data collected by these systems. An essential task in the measure phase is to figure out whether the type of data already available is sufficient for the appropriate analysis to drive problem-solving.
If it turns out that the team needs different data types that are not readily available, then they must work on effective ways of collecting those data. It can be as straightforward as developing a checklist that some employee(s) will fill out using pen and paper or a simple mobile app. Sometimes, it may require collaboration with the IT department to customize software applications to collect the necessary metrics.
The measure phase can be as brief as a day’s work if the data needed is already available, or it could take months if the team decides that it needs to collect new data. Once the team has decided what performance indicators it will use and has a data collection plan, the next step in the DMAIC method is the analyze phase.
LSS practitioners have several quantitative and qualitative techniques in their toolbox to execute the analyze phase, during which they dig deeper into the problems to discover their root causes. It is vital not to fall into the trap of focusing on the symptoms.
Commonly used qualitative analysis tools include:
Commonly used quantitative analysis tools include:
When the team has determined the root causes, it is time to move on to the improve phase.
At the improve phase, the team discusses the potential ways to tackle the root causes of the problem. It is a common practice to prioritize the causes based on a cost-benefit analysis and start with those that offer the most benefit and require fewest resources. As described above, Pareto charts are ideal for determining priorities.
The team develops an implementation plan if they settle on self-evident improvement ideas that won’t require additional analytical analysis to demonstrate their potential effectiveness.
Sometimes, the process is not that straightforward, and the team may decide to run some experiments to study the usefulness of the proposed solution ideas. This approach, called the design of experiments, follows the scientific method, by which analysts work with controlled and independent variables to test their hypotheses. The experiments will reveal whether a proposed solution will offer promising results. The team will then work on an implementation plan.
Implementing the selected solutions can become challenging when they impact several employees’ everyday routines, especially if they are not part of the improvement team. Whether those employees were part of the team or not, management should ensure that they understand why the changes are necessary and how the improved process will boost productivity, making their jobs easier.
The team should also set realistic, measurable targets for the performance indicators and baselines established in the measure phase. Those targets will become essential reference points during the next DMAIC step, the control phase.
The control phase serves three primary purposes:
The team must also continually observe the new process to ensure it is under control. Control charts are widely used to visually track the processes. Control charts offer a reliable means to identify any process abnormalities quickly.
(2) The team must have a systems-thinking mindset that aims to safeguard against harming another process while fixing a part of the system. This holistic approach emphasizes the optimization of the overall system outcomes. Therefore, the team must consider the potential effects of the changes aiming to improve a process on the other interconnected processes.
(3) Team must also consider the sustainability of the process improvements implemented. People generally tend to resist the changes that alter the ways they are used to performing assigned tasks. It is necessary to integrate the changes in the standard operating procedures and train the employees accordingly. A more frequent audit schedule than usual for the improved processes can also be helpful to maintain the changes introduced.
Questions or feedback? Email editor@noodle.com
You can earn Lean Six Sigma certification at the white [...]
Lean Six Sigma applies across industries, including aviation. LSS can [...]
Categorized as: Management & Leadership, Business & Management