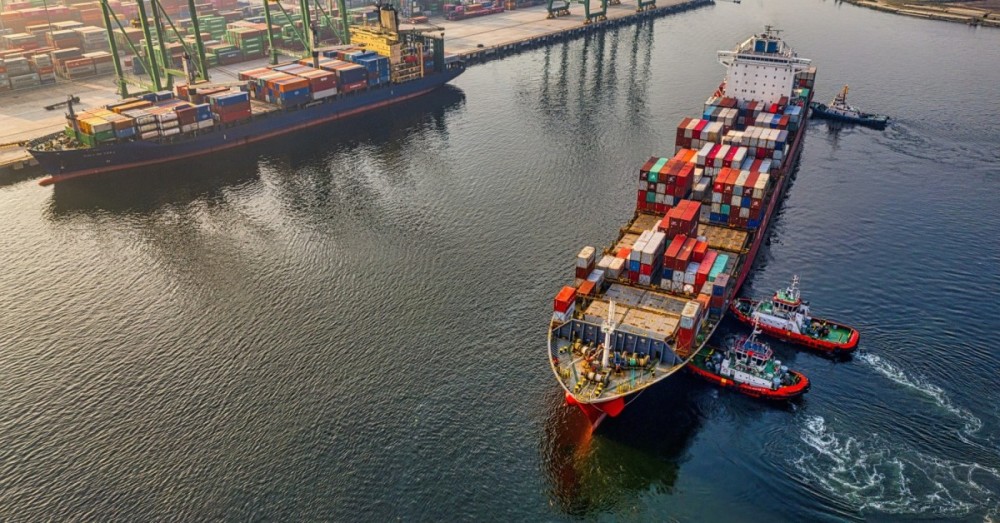
What Is Lean Supply Chain?
Organizations employ lean supply chain management principles to improve profits [...]
The COVID-19 pandemic wreaked havoc on the world’s supply chains. At first, reduced demand helped mitigate some of the problems caused by reduced production and distribution capacities caused by lockdowns and illness.
Eventually, however, consumer demand began to rise. Unfortunately, the supply chain wasn’t strong enough to handle it, leading to delays, lost profits, increased costs, and, in 2022, snowballing inflation.
Many experts blamed China’s strict COVID restrictions. One 2022 Bloomberg article suggests the country’s most recent COVID regulations cause ships to bunch up in key ports. The resulting backlogs had shipping companies struggling to make deliveries; the time required to get products from China to North America increased to over 100 days.
Such congestion isn’t limited to China. The war in Ukraine has European warehouses overflowing. In America, backlogged ports on the West Coast have pushed ships East.
According to the New York Times, the global supply chain infrastructure was precarious even before the pandemic. The rise of online shopping, increased imports, labor shortages, and over-lean practices all weakened the supply chain. When the pandemic hit, strained infrastructure crumbled, leading to major shortages of goods like semiconductors, baby formula, and computer chips. This article explores supply chains during times of crisis and discusses underlying supply chain issues, other supply chain disruptions, and potential solutions.
There isn’t a single supply chain issue causing disruption. Supply chain leaders must address several fundamental problems to mitigate the impact of crises.
Many companies employ lean practices to reduce waste of raw materials and inventory space. Warehouses keep only the goods needed to meet consumer demand in a practice known as just-in-time delivery. Lean thinking can help save money and improve customer satisfaction, but overly lean chains quickly run out of inventory during a crisis.
The pandemic has exacerbated existing labor challenges. According to Third Way, there was atrucker shortage of 80,000 in 2021, the result of truck drivers (just barely) tolerating poor infrastructure and pay for years prior.
Many companies have struggled to entice workers to return after the pandemic. According to a McKinsey study, worker demand is much higher than the supply, driving wages up and leaving positions unfilled. A declining birth rate means labor shortages should continue.
Many companies ran out of steel shipping containers during the pandemic, halting product movement and upending supply chain operations. Not having the proper machinery or storage can cause massive supply chain failures.
Pandemics are not the only potential disruptors to a supply chain. Other crises (both current and in the past) include:
War has a global impact; it drains resources and prevents trade. The war in Ukraine is upending the supply chain, not to mention the lives of millions. It’s eating up European resources and causing bottlenecks in and around the EU. Disruption of the export of Ukrainian grain has caused food shortages worldwide. Many countries have cut themselves off from Russian oil in protest to the war, leading to power shortages.
Natural disasters impact the supply chain, for obvious reasons. A tsunami or hurricane can destroy a port, resulting in massive delays and economic loss. As we begin to feel the impact of pollution, natural disasters will only get worse. Because the supply chain is global, issues in one part of the world can negatively affect another. For instance, flooding in Asia closed a Nissan plant in 2021, meaning cars weren’t produced and could not reach their final destination. Even short-term events can have a long-term impact.
From a macro perspective, rising sea levels have the power to destroy infrastructure (including power lines and highways), causing shutdowns and shipping delays. Cargo and container ships will need new places to dock, meaning companies and governments must allocate more resources to build and improve ports.
Devising an effective response to global supply chain issues is difficult, but experts are working on solutions. Globalization is, in itself, an issue. Unfortunately, centralizing shipping and production is impossible. The answer lies in improving supply chain resilience.
According to Wired, companies benefit from real-time data throughout the production and shipping process. Techniques like location tracking can establish a comprehensive image of the process, leading to targeted plans that address issues and eliminate wasted movement. Improved forecasting makes it easier to predict bottlenecks and reroute goods.
Increased automation can improve supply chain speed. The United Nations Conference on Trade and Development (UNCTAD) notes that automating ports and public border agencies will save time during customs, reducing bottlenecks and human error. One of the rare benefits of the pandemic is that it has sped up the move towards digital infrastructure.
The Harvard Business Review asserts that every supply chain leader should work to identify future vulnerabilities. To accomplish this goal, they need clean data and accurate forecasts. Knowing how a company could react to a shutdown or potential crisis allows leaders to make risk-conscious decisions.
Wages often drive employee retention, as they should. But, McKinsey says the best companies maintain talent by improving all areas of the job, including work-life balance, further education and training opportunities, and internal promotions. These initiatives can improve the company’s image, leading to better results in hiring and retention.
Ultimately, improvements result in more agile supply chains that adapt to market changes. Unlike lean chains that keep inventory on hand, agile chains meet demand with new production. They rely on excellent communication and business relationships more than analytics and forecasting. According to Redwood Logistics, agile chains work best in chaotic markets, such as fashion. Ideally, chains meld the best lean and agile practices.
The answer to this question is: probably. Nobody needs a master’s in supply chain management to work in the field, or even get a good job. However, you may need one for management positions. At the very least, a master’s can help you stand out from the crowd of applicants.
Most supply chain management (SCM) professionals who want a graduate education pursue either a Master of Science (MS) or a Master of Business Administration (MBA) with an SCM concentration. The main difference between these degrees is MBA programs typically lead to general management careers. They include traditional business coursework like accounting and leadership training, plus SCM coursework.
The University of Tennessee Executive MBA (designed for experienced professionals) prepares graduates for upper-level management positions, including running companies and making decisions. These are the people who change the supply chain infrastructure.
MS degrees also prepare graduates for upper-level positions, but typically in a specific sector, such as procurement or shipping. The University of Tennessee Master of Science covers general SCM topics, such as planning, data modeling, and strategy.
Questions or feedback? Email editor@noodle.com
Organizations employ lean supply chain management principles to improve profits [...]
We've compiled a guide to the best Master of Science [...]
Categorized as: Supply Chain Management, Business & Management